Domestic Automobile Parts Manufacturer
Establishment of Smart Factory
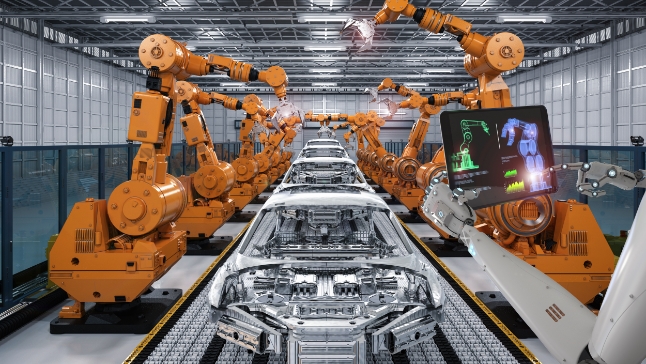
""The company was able to enhance competitiveness of product quality by obtaining the information of input material, operation information of facilities, disorder information of facilities and detailed LOT tracking related to workforce, which is related to the manufacturing of the highly value added products that are directly related to car safety. In addition, the company can now provide the integrated management for the quality information of partners’ shipping during warehousing and inspection information at the time of import." "
Domestic Automobile Parts ManufacturerChallenge
Company A, a domestic automobile parts manufacturer, needed diversification in customers. In order to guarantee the product quality,
Europe and the U.S require parts providers to achieve IATF 16949 (a standard for international quality management system), which needs to be included on the contract when providing their products.
IATF 16949 general discusses the overall process of companies.
In automobile manufacturing, however, it is now essential to provide detailed LOT traceability regarding materials, facilities and workforce that are needed for product manufacturing. Therefore, a smart factory needs to be introduced for system of collecting relevant information.
IATF 16949 general discusses the overall process of companies.
In automobile manufacturing, however, it is now essential to provide detailed LOT traceability regarding materials, facilities and workforce that are needed for product manufacturing. Therefore, a smart factory needs to be introduced for system of collecting relevant information.
Solution
Company A, a domestic automobile parts manufacturer, needed a system that provides information and solutions in three layers of stakeholders: management, manager and user.
1) Company A collects facility information for the entire lines real time by establishing the infrastructure environment where facility information can be collected regarding the entire lines on site among manufacturing line for car motors.
2) Based on that, the company has established a smart manufacturing operation system regarding manufacturing, quality.
ㆍProvide flexible expandability in the case of facility changes through I/F standardization from various facility sources.
ㆍRealize I/F standardization that organically goes along with neighboring systems to realize processes on ERP regarding manufacturing plan and estimated material warehousing information, quality information of partners’ shipping when warehousing materials, manufacturing performance and shipping performance based on the ERP standard information.
ㆍEnhance user convenience by linking import inspection → process inspection → shipping inspection while reflecting various checklist (sheet) on the system.
ㆍSecure visualization on site and for management such as comprehensive dashboard and various KPI Report.
Identify manufacturing status in real - time and secure manufacturing visibility
-
Material Handling, Production, Quality, Equipment
Monitoring for Working, Check Sheet, Quality Monitoring, Quality Management for each steps, Alarm management
- Plan (ERP) : LOT Management for each process (synch with material data) → Shipment (ERP) → Product Warehouse → Product → Production Line (Process/Quality) → Material
-
Material Quality :
- Material Warehouse → Process Material → Input Material → ... → Test → Inspection → Product Warehouse → Product → Production Line (Process/Quality) → Material
- Input Material using Barcode, Automated EQP data gathering, EQP management, Consumable exchange
Benefit
Company A, a domestic automobile parts manufacturer, has applied process realignment and a new system throughout the entire manufacturing for 30 factory lines nationwide. The new application includes manufacturing index, on-site monitoring, quality inspection management (e.g. importing, process, shipping and
products with faulty), warehouse management (e.g. materials, products), process management (input, manufacturing performance, document creation by manual work), LOT diagram (traceability), quality analysis (SPC) and facility management.
As a result, the company has established the ground for improving work efficiency, preventing user error and finding out/tracking manufacturing process information.
In particular, the real-time monitoring becomes available for active/standby lines and disorder information.
The new solution also minimizes delay in manufacturing and shipping to clients due to the lack of materials, which contributes to productivity improvement and stable delivery.